Why People are Changing from Ni-Hard to High Chrome White Iron
January 23, 2024
onHistory of Both Ni-Hard and High Chrome White Iron
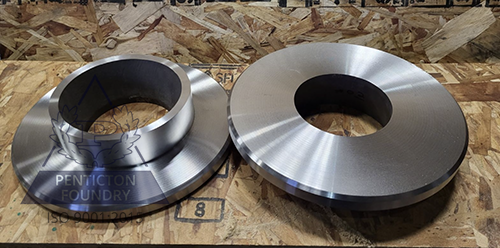
To understand why people are changing from Ni-Hard to high chrome white iron (HCWI) it is important to know the history of both alloys.
High chrome white iron was discovered in 1915. In the mid-1920’s, scientists at the International Nickel Company (INCO) discovered that a mixture of Ni and Cr added to cast iron produced an alloy that was resistant to abrasion in the as-cast condition. It had a microstructure of austenite and martensite. INCO trademarked this alloy Ni-Hard and promoted it worldwide. It could be melted in a cupola – a major benefit – as high chrome white iron alloys had to be melted in an electric furnace. This benefit made Ni-Hard the most mass-produced abrasion resistant alloy in the world.
After 1920, the Electro Metallurgical Company made castings in the 15% - 35% Cr range to reduce maintenance costs in their own crushing and grinding operations. They marketed these new alloys in an effort to sell more of their ferrochromium. As these alloys couldn’t be melted in a cupola, they were not produced in the quantities that Ni-Hard was.
The Start of the Change
People started to notice that the high chrome white iron alloys were:
- Less brittle than Ni-Hard
- Usually more abrasion-resistant
- Always more corrosion-resistant
- This opened up a world of applications for high chrome white iron, especially in the pump industry
Problem: In the as-cast condition, heavy section high chrome white iron wasn’t always uniform in wear-life. Ni-Hard castings, made to spec, had consistent life spans, no matter what the section thickness was. This unpredictability meant Ni-Hard had an advantage over high chrome white iron for thick section castings for many years. The advantage disappeared when proper heat treatment for high chrome white iron was developed.
Resource: Read this resource for tips on “How to Heat Treat High Chrome White Iron.”
The Improvements in High Chrome White Iron
- In the early 1960’s, much work was done to change the chemistry of high chrome white iron and alter its microstructure and improve the abrasion-resistance of thick section castings
- In the 1970’s, work was done to minimize the amount of retained austenite in the HCWI alloys
- It was discovered that premature failure was minimized when hardness was maximized
Advantages of High Chrome White Iron vs Ni-Hard
Ni-Hard was popular because it could be melted in a cupola, and it could be cast in almost any section thickness. For years it was the go-to alloy for most high wear applications. Now, with most foundries melting high chrome white iron in electric furnaces, and heat treating techniques being perfected, high chrome white iron has become much more popular than Ni-Hard.
- High chrome white iron alloys are more corrosion-resistant than Ni-Hard
- Heat treatment makes high chrome white iron castings consistent throughout their section thickness. Ni-Hard no longer has this advantage
- Normally, high chrome white iron is harder and more abrasion resistant than Ni-Hard
- Often, high chrome white iron is less brittle than Ni-Hard and has a higher tensile strength
- Depending on commodity prices, high chrome white iron is less expensive to melt than Ni-Hard because of Ni-Hard’s high nickel content
Still Unsure When to Switch?
Nine times out of ten, when we get a request for Ni-Hard, the drawing referred to is from the 1950’s or 1960’s. During that time, Ni-Hard was a good choice. Since then, the performance of high chrome white iron alloys has improved thanks to metallurgists, foundry people and scientists who have studied it and made changes.
Examples of parts we have recently changed from Ni-Hard to HCWI include:
- Bucket lip liners
- Bucket teeth
- Extrusion augers
- Extrusion sleeves
- Cement pumper elbows
- Asphalt and concrete recycler parts
Read: To learn more about high chrome white iron please see our Abrasion Resistant Cast Irons page.