Ductile Iron – Heat Treating vs Alloying
on April 10, 2018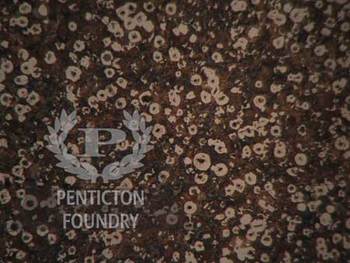
When designing with ductile iron as an engineer you may notice that almost all ductile iron standards don’t specify a chemistry requirement. This is because the microstructure and mechanical properties can be achieved in different ways. Specifically, the mechanical properties can be affected by:
- Changing the chemistry
- Heat treating techniques
Charge materials
Scrap chemistry and quality have a big effect on ductile iron quality. This is because the level of tramp elements affects the microstructure and mechanical properties. One recommendation is to use pig iron with low tramps.
Ductile Iron Treatment
The method of treatment affects the quality of the iron. Ideally, the method used would allow the reaction to be very controlled. It would lead to a high Mg recovery, as well as a good nodule quality and high nodule count. It’s important to work closely with the treatment alloy supplier to determine what works best for the foundry process.

Heat Treatment
Altering the microstructure and mechanical properties can be done by heat treating. A casting alloyed to meet the 65-45-12 specification can be heat treated to meet the 60-40-18 material properties. The 65-45-12 material can also be heat treated to meet the 80-55-06 properties. Heat treating to achieve properties improves the delivery time and the final cost.
Summary
- Every foundry will make ductile iron the way that works best for them
- Using low tramp charge materials and a controlled Mg treatment process, one can pour 65-45-12 material that also crosses over to the 60-40-18 requirement without heat treating
- Sourcing good charge materials and working closely with suppliers can improve ductile iron quality and potentially shorten the casting delivery times.
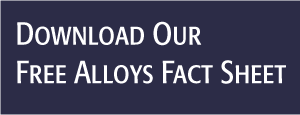