Casting Design Development Process
July 11, 2024
onTo ensure that a casting or part performs to expectations, a successful collaboration between the customer, foundry and engineering (design) firm must occur. This blog offers tips and troubleshooting to facilitate this collaboration.
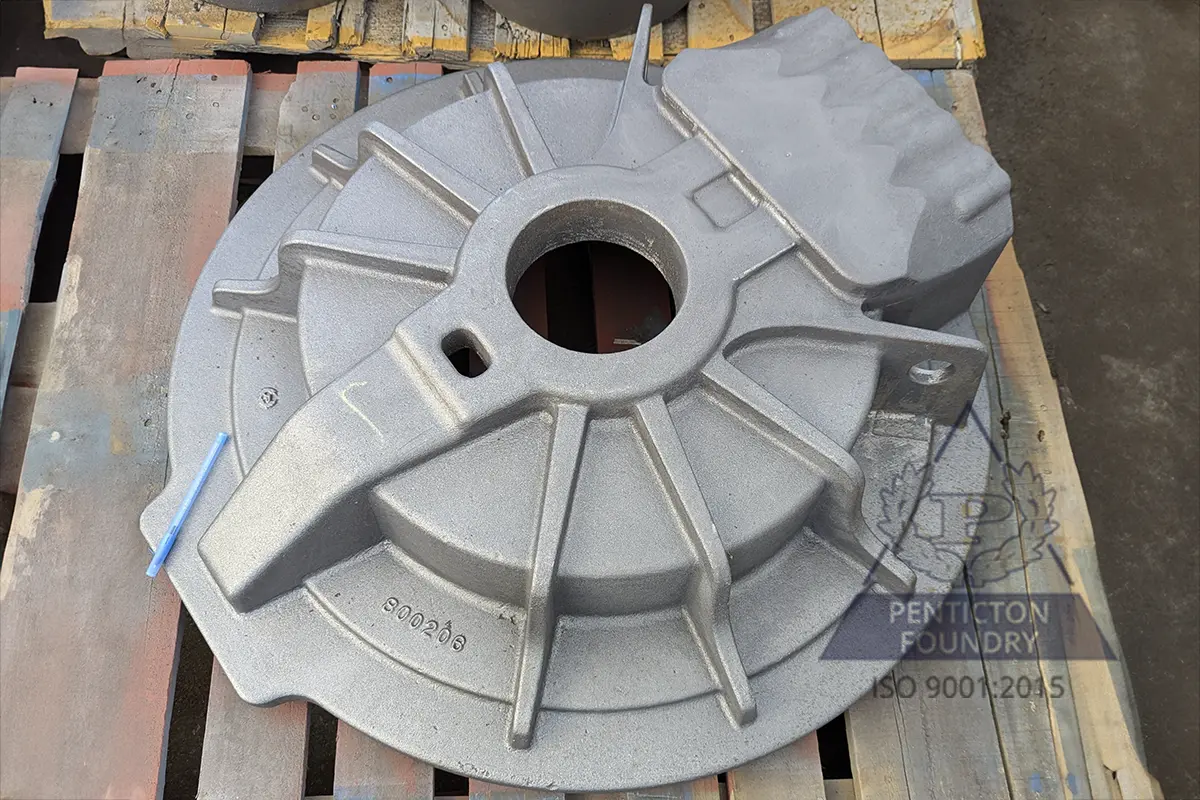
General Components of Success
1) Communication must be transparent
2) Is there a specific challenge that is being addressed by this part? For example, a wear challenge?
3) Will the design address the specific challenge? Foundries can often serve as design partners in the process
4) Accept that many iterations may be required, even before pattern (tooling) construction begins
5) The foundry should use a modelling software to validate the design. This will ensure that the casting is formed properly and solidifies correctly. Specifically, it will prove the casting design and also the gating/risering (rigging) that will be used
6) When designing a casting, design engineers must consider the fact that molten metal travels through the mould, fills the mould and solidifies (directional solidification) in the mould.
Specific Design Considerations
There are several specific design considerations that should be explored during the initial conversations between the foundry, customer and engineering firm:
1) Geometries affect the final structure. Design with radii and round corners, avoiding sharp transitions and angles
Resources: The Top 5 Design Mistakes in Chrome White Iron Castings is worth a read, as is The Top 5 Design Mistakes in Ductile Iron Castings.
2) If ribs and gussets are needed for strength, the foundry can help with location, size and shape
3) Bringing too many sections/members together into the same junction will cause hotspots. Avoid this mistake
4) If possible, keep section thickness uniform. If section thickness does need to change, blend the different areas together smoothly
5) Ribs and webs need to be the correct location, thickness and orientation
6) Watch out for lugs and bosses. Keeping their section thickness uniform and avoiding hotspots is beneficial
Pro Tip: Holes may be needed. Discussion should ensue to decide if the holes can be cored, or if they should be machined in after the fact (keep in mind, that chrome white iron can be machined)
Additional Questions/Areas the Foundry Will Be Considering
1) Troubleshooting the castability of the part:
- Will there be hot spots?
- Will the metal freeze directionally?
- Are cores needed?
- Are loose pieces needed?
- Can the casting be fed properly?
- Should any parts of the mould or cores be 3D printed?
- The considerations are vast, which is why communication is key
2) How will the casting solidify based on the metal it is poured in and its shape?
3) How will the casting shrink dimensionally? The pattern must be larger to account for this dimensional change
4) Will the constituents formed in the microstructure of the casting during solidification be what the customer needs? If required, can they be altered after solidification?
5) After solidification, will the casting have the required strengths and function as it is intended?
Fundamentally, if the customer, engineering (design) firm and foundry are working together, the resulting casting will meet or exceed the requirements. Don’t hesitate to go back to the drawing board and run the simulation again after seeing the real world results on the foundry floor. Slight changes can improve the castability and ultimately the quality of the casting.
Read: This infographic offers a checklist to facilitate a successful working partnership between a foundry and customer.