Advantages of the Casting Process Compared to the Fabrication Process
on November 23, 2016There are a number of advantages that the casting process offers when compared to the custom metal fabrication process. For example, welding during the fabrication process creates more stress and distortion due to localized heat. Casting, on the other hand, creates a more homogeneous microstructure as there is no heat affected zone. In addition, a higher-quality end product can result from the casting process. This is due to a number of factors:
- The ability to transition material thicknesses and add a number of radii that reduce stress
- Once a pattern is approved each casting is the same, versus a fabrication where human error is involved and parts can be assembled incorrectly
- It’s possible to cast complex dimensions, shapes and sizes
- Converting a steel fabrication to a ductile iron casting also offers machinability advantages
- Ductile iron has greater vibration damping properties
There are also significant cost savings to be realized due to the following:
- Casting eliminates many processes, reducing production time
- Multiple castings can be made at one time
- Less skill is required as casting production can be more automated, as opposed to the skills required for welding and fabrication
- More efficient use of material as “drops/crops” are not part of the material cost – material costs are lower when using ductile iron as opposed to steel fabrications
Read: For more information on ductile iron vs steel, read this blog.
Ultimately, when considering the custom metal fabrication process versus the casting process, it’s evident that there are significant advantages that the casting process offers both in terms of quality control and cost savings.
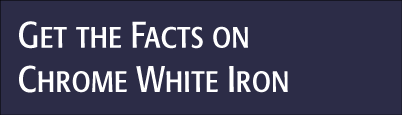