30% Chrome White Iron Data Sheet
on April 18, 201930% Cr Corrosion Resistant Alloy
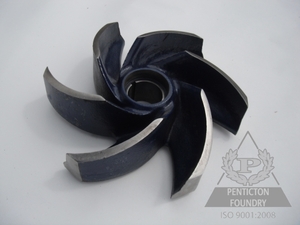
The 30% Cr alloy is designed for use in applications like flue-gas desulfurization (FGD). The higher Cr content makes this alloy especially useful when conditions of severe acid corrosion exist and when high Cl ion concentrations are present.
Read this, to find out why chrome white iron is so abrasion resistant
Note: Technically, this alloy does not fall into an ASTM A532 specification because the Cr is higher than 30%.
Composition
|
C |
Mn |
Si |
Cr |
Mo |
Min% |
2.1 |
|
|
30 |
|
Max% |
2.5 |
1.0 |
1.0 |
32 |
1.0 |
Typical Range of Physical and Mechanical Properties (reference Abrasion Resistant Handbook)
Density lb/in3 (g/cm3) |
0.26 (7.6) |
Thermal Conductivity Btu/hr·ft·F (W/m·K) |
8.6-17.3 (15-30) |
Specific Heat at 70F Btu/lb·F (J/Kg·k) |
0.119 (500) |
Coefficient of Thermal Expansion Ɛ/F(Ɛ/C)X106 average between 70-1112F (10 – 600C) |
7.2 (13) |
Melting Temperature (F) |
~2400 F |
Compressive Strength Ksi (MPa) |
429 (2960) |
Transverse Strength Ksi( MPa) |
136 (938) |
Modulus of Elasticity Mpsi (GPa) |
31-33 (215-230) |
Typical Hardness
|
Brinell (depends on thickness) |
As-Cast |
~500 |
Hardened |
>600 |
Applications
This alloy is especially designed for use in applications like flue-gas desulfurization (FGD). It is used to make pump parts like volutes, impellers and liners.
It also works well in marine atmospheres, in numerous salt solutions, in organic acid solutions, and in industrial atmospheres (like the papermaking industry).
Corrosion Resistance
This alloy has good corrosion resistance in oxidizing environments and some reducing environments. This is because of its high Cr content, which ensures that a passive film forms on its surface in corrosive environments. The alloy also has resistance to stress corrosion cracking. It is not, however, as abrasion resistant as other 25% Cr alloys due to its ferritic matrix.
Processing
a) This alloy is typically supplied in the hardened condition.
b) It can be fully machined.
c) Often, inserts can be cast in to facilitate drilling and tapping. This will save some money, but may impact corrosion resistance due to galvanic corrosion.
Read: To learn about other ASTM A532 alloys, check out our chrome white iron webpage.